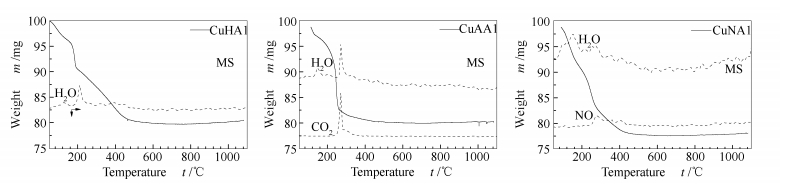

Citation: QIN Fa-jie, LIU Ya-jie, QING Shao-jun, HOU Xiao-ning, GAO Zhi-xian. Cu-Al spinel as a sustained release catalyst for H2 production from methanol steam reforming:Effects of different copper sources[J]. Journal of Fuel Chemistry and Technology, 2017, 45(12): 1481-1488.

甲醇制氢铜铝尖晶石缓释催化剂的研究-不同铜源合成的影响
English
Cu-Al spinel as a sustained release catalyst for H2 production from methanol steam reforming:Effects of different copper sources
-
Key words:
- solid-state reaction method
- / solid solution
- / methanol steam reforming
-
氢能源没有含碳化合物的排放,对环境无害,因而是一种极其适合的新能源[1]。制取氢气方法很多,如水电解[2]、烃类水蒸气转化[3]、水煤气变换[4]、氨分解[5]、甲醇制氢[6]等,其中,甲醇制氢具有明显的竞争力,主要体现在以下几点:甲醇具有氢能量密度高、含碳量低、容易获得与存储等特点[7];甲醇制氢成本低、条件温和、无腐蚀;产物氢气含量高(体积分数最高可达75%),无NOx、SOx等排放。甲醇制取氢气的途径有:裂解[8]、水蒸气重整[9]、部分氧化[10]、氧化重整[11]。甲醇水蒸气重整(MSR)制氢技术具有最大的氢气收率(3 mol H2/1 mol甲醇),除了甲醇中的2 mol H2外,还得到水中的1 mol H2。
应用于甲醇水蒸气重整的催化体系大体可以分为Ⅷ-Ⅹ族贵金属和Cu基催化剂[7],其中,Cu基催化剂因成本低、活性好、选择性高等优点而成为研究和应用最多的催化剂[12],包括Cu/ZrO2[13]、Cu-ZnO[14]、Cu/CeO2/ZrO2[15]和Cu基尖晶石[16]等。
尖晶石以AB2O4表示,由占据四面体位置的二价金属离子(A2+)和占据八面体位置的三价金属离子(B3+)形成的一种立方晶格氧化物[17]。对Cu基尖晶石而言,铜离子稳定在氧化物晶格结构中,为还原活化获得高分散的铜提供了可能。文献研究表明,铜基尖晶石催化剂由于其结构特殊,能够提高铜的分散度,且对铜的烧结具有较好的抑制作用,从而表现出较好的催化活性和稳定性[18]。Matstukata等[19]在研究Cu/Al2O3时发现,高温焙烧后形成了Cu-Al尖晶石结构,经300 ℃还原预处理后其对甲醇重整具有更高的活性和稳定性。Fukunaga等[20]通过柠檬酸络合法制备的Cu-Mn催化剂,900 ℃焙烧形成的Cu-Mn尖晶石经250 ℃还原后获得较小的金属Cu粒子(-11 nm),其活性明显高于300 ℃焙烧的非尖晶石催化剂。Pussana等[21]研究了CuCr2O4、CuMn2O4和CuFe2O4在含氧烃类化合物水蒸气重整制氢反应中的催化剂性能,与商业Cu/ZnO/Al2O3相比,具有尖晶石结构的催化剂均表现出优异的催化性能。在所有已报道的Cu-基尖晶石当中,Cu-Al尖晶石比其他尖晶石(比如Cu-Fe、Cu-Cr、Cu-Mn、Cu-La尖晶石等[22, 23])在MSR中表现出更高的催化活性。
通过分析发现,已有的研究中铜基尖晶石催化剂在使用前均经过了预还原处理。在还原过程中,铜会发生烧结长大,从而导致活性的损失。针对此问题,本课题组采用不进行预还原的方式,首先探索了柠檬酸络合法制备的CuAl2O4、CuFe2O4、CuCr2O4三种铜基尖晶石催化剂。结果表明,催化剂在使用前不经过预还原处理,在反应过程中活性铜逐步释放,最终表现为催化剂活性先增加后减小的现象。由于该方法制备的催化剂比表面积较小,催化性能一般[22]。为了提高催化剂的比表面积,研究了固相法合成的CuAl2O4尖晶石催化剂,其比表面积得到了显著提高[24, 25]。研究证实催化剂中少量的CuO可以启动反应,CuAl2O4逐渐释放活性Cu,催化活性呈先增加后缓慢降低的趋势。进一步深入的研究表明,Cu/Al比、焙烧温度等因素对固相法合成铜基尖晶石的结构及其缓释催化性能均有较大的影响[25]。
为了丰富铜基尖晶石缓释催化材料的合成化学,获得微观结构变化与催化性能之间的关系,本研究拟以氢氧化铜、乙酸铜和硝酸铜等为铜源,通过固相法合成CuAl2O4尖晶石催化剂,结合表征和甲醇重整反应性能评价,考察了不同铜源的影响,获得了对合成甲醇重整缓释催化材料的新认识,为进一步研究与开发高效铜铝尖晶石缓释催化剂提供基础数据。
1 实验部分
1.1 实验原料
氢氧化铜(含量98%)、乙酸铜(分析纯,含量99.0%)、硝酸铜(分析纯,含量99.5%)、拟薄水铝石(Al2O3含量71%)、甲醇(化学纯,含量99.95%)、蒸馏水。
1.2 催化剂的制备与成型
催化剂采用固相法合成,合成原料配比及温度条件选取本实验室优化结果,以比较不同铜源的影响。具体过程为:将不同Cu源和拟薄水铝石按Cu/Al物质的量比为1:3先均匀混合,然后球磨6 h,最后放入马弗炉中以3 ℃/min升温至950 ℃焙烧0 h(即不保留时间)得到催化剂。将氢氧化铜、乙酸铜和硝酸铜为原料制备的前体分别标记为CuHAl、CuAAl和CuNAl,焙烧后得到的催化剂相应的标记为CuHAl-950、CuAAl-950、CuNAl-950。在催化剂中掺入质量分数3.0%的石墨,混合均匀后,压片成型。
1.3 催化剂的表征
催化剂的物相结构用Bruker公司的AXS D8衍射仪表征,Cu Kα射线(λ = 0.154 06 nm),管电压40 kV,管电流40 mA,步长0.02°,扫描速率5 (°)/min,10°-80°扫描。
Cu L3-edge XANES表征在北京同步辐射的4B7B-软X射线实验站测定。催化剂的比表面积在JW-BK122W型比表面积及孔径分析仪上分析,用液氮保温,N2作为吸附质。
程序升温还原(H2-TPR)在FINESORB-3010型多功能吸附仪上进行。样品装量30 mg,还原气10% H2/Ar,热导检测(TCD)。样品首先在Ar气氛中300 ℃处理30 min,降至室温后,切换为还原气(15 mL/min),吹扫至基线稳定后,以10 ℃/min升温至900 ℃。
热重-质谱(TG-MS)分析在HCT-2型微机差热天平和在线质谱仪上进行,测试25-1 100 ℃,升温速率为10 ℃/min,空气流量为100 mL/min。
反应后催化剂中金属铜的比表面积(ACu)在FINESORB-3010型多功能吸附仪上进行N2O化学吸附(N2O-adsorption)测定。催化剂用量为30 mg,催化剂先在氧气气氛下,280 ℃氧化30 min,降至室温;然后切换10% H2/Ar(15 mL/min),吹扫至基线稳定后,以10 ℃/min程序升温至280 ℃,使CuO完全还原,在此气氛下降温至30 ℃;接着在30 ℃下切入5% N2O/Ar(15 mL/min),以1 ℃/min程序升温至50 ℃,保留20 min;然后直接切入10% H2/Ar(15 mL/min)吹扫30 min,再以3 ℃/min程序升温至280 ℃进行还原。铜的比表面积可以用下面的公式计算:
式中,X和Y分别代表CuO和Cu2O消耗H2的量;Nav为阿伏伽德罗常数,MCu=63.546 g/mol;1.4 × 1019是铜平均面积为0.071 1 nm2的表面原子数。
1.4 催化剂的评价
催化剂的性能评价在连续的固定床装置上进行。催化剂用量为2.5 g,粒径为8-14目。反应原料为44%甲醇水溶液,进料使用2ZB-1L10双柱塞微量泵。反应在压力1.0 MPa、温度255 ℃,质量空速2.18 h-1的条件下进行。催化剂无需预还原处理,当反应器升到指定温度后,开始进料反应。产物经冷凝后取气体样品和液体样品进行色谱定量分析,采用GC-960型气相色谱仪(TDX-01柱,TCD)和GC-960型气相色谱仪(Porapak-T柱,TCD)分析产物中的H2、CO、H2O、CH4、CO2、CH3OH、MF(甲酸甲酯)和DME(二甲醚)。
2 结果与讨论
2.1 新鲜催化剂的表征
2.1.1 TG-MS表征
催化剂前体的TG-MS分析结果见图 1。由图 1可知,CuHAl、CuAAl、CuNAl样品的主要失重温度依次为190-600、130-600和190-600 ℃。可见三种催化剂前体的失重温度都发生在600 ℃之前,三种样品的失重率依次为20.1%、40.0%和44.8%,基本上接近理论值。
对于CuHAl样品,质谱检测到两个H2O的信号峰正好对应于两个失重阶段产生的水。第一步失重出现在50-190 ℃,主要为物理吸附水的脱除;第二步失重出现在190-600 ℃,为拟薄水铝石脱水和Cu(OH)2的分解。与纯Cu(OH)2的TG-MS分析结果比较,CuHAl的分解温度与纯Cu(OH)2的差别不大,说明氢氧化铜在球磨过程中变化不明显。
CuAAl样品出现多个明显的H2O信号峰和一个CO2信号峰,在50-200 ℃为物理吸附水的脱除;200-600 ℃为Cu(CH3COO)2的分解以及拟薄水铝石脱水。比较起始分解温度,CuAAl的分解温度比纯Cu(CH3COO)2·H2O的分解温度低约30 ℃,说明乙酸铜在球磨时发生了一定程度的分散或变化,使得其容易分解。
CuNAl样品第一步失重出现在50-190 ℃,为物理吸附水和硝酸铜结晶水的脱除;190-600 ℃为Cu(NO3)2的分解和拟薄水铝石脱水,因此, 在两个失重阶段范围内可以看到明显的H2O信号峰和NO信号峰。比较起始分解温度,CuNAl的分解温度比纯Cu(NO3)2·3H2O的分解温度低约60 ℃,说明球磨使硝酸铜发生一定的变化。
以上数据表明,三种催化剂前体在600 ℃之前都可以完全分解转化为氧化物,之后形成尖晶石。
2.1.2 XRD表征
前期研究以氢氧化铜和拟薄水铝石为原料,固相法合成条件优化试验表明Cu/Al=1:3时的最佳温度为950 ℃,所得Cu-Al尖晶石作为甲醇重整制氢缓释催化剂呈现优异的效果。为进一步探索固相合成作用机制及其对催化性能的影响,在相同条件下改变铜源进行了研究。
不同铜源制备催化剂CuHAl-950、CuAAl-950和CuNAl-950的XRD表征结果见图 2。
由图 2可知,所得XRD谱图未发现CuO的衍射峰,其特征衍射峰与卡片PDF#78-1605相同,只是对应2θ有所增大,归属为尖晶石结构。分析发现,三个尖晶石样品衍射峰的相对强度和峰宽的差别不大,这些结果表明催化剂的物相组成未因合成原料的不同而改变。
根据谢乐公式计算出CuHAl-950、CuAAl-950和CuNAl-950催化剂中尖晶石相的平均晶粒粒径(取(220)、(311)、(400)、(422)、(511)、(440)六个晶面主要衍射峰的平均值),具体见表 1。CuHAl-950中尖晶石粒子最大,约12.7 nm,CuNAl-950的最小,约11.3 nm。
Fresh catalyst CuHAl-950 CuAAl-950 CuNAl-950 Cu source Cu(OH)2 Cu(CH3COO)2·H2O Cu(NO3)2·3H2O dspinel/ nm[a] 12.7 12.4 11.3 BET surface area A/ (m2·g-1) 65.9 33.8 25.4 Pore volume v/(cm3·g-1) 0.434 0.213 0.289 X spinel / %[b] 81.3 79.1 93.7 x in Cu1-3xVxAl2+2xO4 0.129 0.134 0.104 After MSR CuHAl-950-t CuAAl-950-t CuNAl-950-t dCu-after MSR / nm[c] 6.6 9.2 20.2 Cu0 surface area A/(m2 ·g-1)[d] 183.9 146.1 94.7 RD/%[e] 88.7 85.9 66.8 [a]: the crystallite size of spinel was calculated by the Scherrer equation with the XRD patterns (Figure 2);
[b]: the molar ratio of Cu in the Cu-Al spinel phase to total Cu as derived from H2-TPR (Figure 5);
[c]: Cu crystalline size of tested catalyst was calculated by the Scherrer equation with XRD patterns (Figure 8);
[d]: Cu surface area of tested catalyst was measured by N2O chemisorption method;
[e]: the releasing degree (RD) of Cu from spinel after catalytic testing was calculated by using H2-TPR data of tested samples利用XRD数据计算出CuHAl-950、CuAAl-950和CuNAl-950中尖晶石的晶胞常数a分别为0.804 0、0.805 1、0.805 8 nm,与文献中的CuAl2O4(PDF#78-1605,a=0.807 9 nm)对比可知,三个尖晶石的晶胞常数a值要小一些。根据拟薄水铝石高温下转化为γ-Al2O3也具有尖晶石结构的事实,所合成样品形成了非计量尖晶石结构即固溶体,可以表示为Cu1-3xVxAl2+2xO4(V=vacancy),其中, x值可以由H2-TPR数据得到(表 1)。
总之,三种铜源都可以合成出尖晶石,其晶粒粒径相差不大,晶胞常数有一定差异。
2.1.3 Cu L3-edge XANES表征
为了研究催化剂表面及近表面Cu的化学状态,对新鲜催化剂进行了Cu L3-edge XANES表征,结果见图 3。
图 3中所有的吸收峰都归属于Cu2+的2p3/2→3d跃迁[26]。与CuO的吸收峰(931.3 eV)相比,CuHAl-950、CuAAl-950和CuNAl-950催化剂的吸收峰向低能量方向移动,分别为929.5、930.0、929.9 eV。根据前人的研究,不同的铜配位环境测得的吸收峰有明显的位移,尖晶石中四配位和六配位分别为930.1和930.8 eV,均比CuO的931.3 eV小[27]。因此,所测结果表明,三种催化剂表面尖晶石的Cu2+的分布有明显的差异。CuHAl-950催化剂表面尖晶石结构中含有最多的四配位铜,而CuAAl-950和CuNAl-950催化剂表面尖晶石含更多的六配位铜。这表明不同铜源制备的催化剂表面Cu物种的微观结构不同,从而具有不同的表面性质。需要指出的是表面尖晶石Cu物种的精细结构主要由合成原料的不同而导致,与尖晶石含量没有直接关系(具体见表 1)。
2.1.4 BET表征
不同铜源制备的新鲜催化剂的孔径分布、比表面积以及孔体积见图 4和表 1。
由图 4可知,新鲜催化剂都具有较宽的孔径分布,为2.4-144.3 nm。CuAAl-950催化剂的孔径分布呈单峰特征,最可几孔径约为11.7 nm。CuHAl-950和CuNAl-950催化剂的孔径分布呈双峰特征,其中, CuHAl-950分别为2.4-8.9 nm和8.9-126.6 nm,CuNAl-950分别为3.0-12.1 nm和12.1-138.0 nm。可见采用不同铜源合成的尖晶石固溶体,其孔分布存在着明显的差异。
由表 1可知,三种催化剂的比表面积大小顺序为CuHAl-950>CuAAl-950>CuNAl-950,孔容的大小顺序为CuHAl-950>CuNAl-950>CuAAl-950。可见,不同铜源制备的催化剂比表面积、孔容和孔径相差较大,没有呈现出规律性,其中, Cu(OH)2原料制备的催化剂最好,具有最大的孔容和比表面积。
2.1.5 H2-TPR表征
为了考察催化剂在甲醇重整反应中活性组分的还原难易程度,对新鲜催化剂进行了H2-TPR表征,具体见图 5。根据本课题组的研究,固相法制备的尖晶石在100-900 ℃呈现多峰分布,大致可分为三部分:α(160-280 ℃)、β(280-500 ℃)、γ(500-900 ℃),依次归属为非尖晶石结构的CuO物种[28]、易还原的尖晶石结构Cu物种、难还原的尖晶石结构Cu物种。
由图 5可知,三种催化剂呈现不同的还原性能。CuHAl-950和CuAAl-950的还原峰及其位置差异较小,而CuNAl-950中尖晶石还原峰温(480 ℃)明显高于前两者,可见不同的铜源对催化剂的还原性能影响较大。
根据还原峰面积计算CuHAl-950、CuAAl-950、CuNAl-950中尖晶石含量依次为81.3%、79.1%、93.7%(表 1),可知以氢氧化铜和乙酸铜为铜源时所得催化剂中尖晶石含量差别较小,而以硝酸铜为铜源时所得催化剂中尖晶石含量较高,表明不同铜源对尖晶石的生成也存在明显影响。
对催化剂的H2-TPR还原谱图(图 5)进行累计积分处理,获得还原度随还原温度的变化曲线,见图 6。可知,三种催化剂的还原行为有明显的不同,CuHAl-950最容易还原,最大速率在400 ℃左右;CuAAl-950最大速率在420 ℃左右;CuNAl-950则最难还原,最大速率在520 ℃左右。在450 ℃时,CuHAl-950、CuAAl-950和CuNAl-950能还原Cu2+分别为69%、56%和27%。由此可见,CuNAl-950催化剂很难还原。
2.2 催化剂的性能评价
以甲醇水蒸气重整制氢为探针反应,考察了不同铜源制备的三种催化剂的催化性能,结果见图 7。
由图 7可知,CuHAl-950催化剂具有最高的初始催化活性,并随着反应的进行,催化活性先逐步上升后缓慢下降,最终达到基本稳定,符合缓释催化剂的特征。CuAAl-950催化剂的初始催化活性也比较高,随后其催化活性快速下降,随着反应的进行,活性波动不是很大,表明该催化剂也具有较好的稳定性。而CuNAl-950催化剂的活性极低,反应176 h后几乎没有活性。可见,由不同铜源制备的铜基尖晶石催化剂在催化活性上表现出较大的差异,CuHAl-950表现出最好的活性和稳定性。
根据前期研究,在甲醇重整反应过程中,CuO物种先在低温条件下启动反应[25],随后尖晶石逐渐缓释活性铜而起催化活性。显然,催化活性的巨大差异与催化剂中非尖晶石CuO的含量以及固溶体的还原难易程度有关(图 6)。对于稳定性而言,则与活性Cu的稳定性有关,详细细节有待进一步研究。
为了获得反应后催化剂中尖晶石的留存结构以及缓释出来铜的特征,对其进行了XRD表征,具体见图 8。
由图 8可知,三个反应后的催化剂除了金属Cu和尖晶石衍射峰外,还有石墨的特征峰,其中, 石墨是成型时添加的,金属Cu是在反应过程中通过铜离子原位还原释放形成的。反应后催化剂留存结构仍呈现尖晶石的衍射峰,表明经长期(175-300 h)反应评价后,形成缺陷尖晶石结构。与新鲜样(图 2)对比可知,反应后尖晶石的衍射峰的强度变弱,且衍射峰向大角度方向偏移,表明催化剂中尖晶石的结构参数因铜的缓释而发生了变化。
通过谢乐公式计算出反应后催化剂中Cu的晶粒粒径(表 1)可知,CuNAl-950-t、CuAAl-950-t、CuHAl-950-t中的Cu粒子粒径依次为20.2、9.2和6.6 nm,对应的Cu比表面积分别为94.7、146.1和183.9 m2/g(表 1),这与催化活性依次增大的顺序是一致的。另外,根据50 h的活性和比表面积计算得到的比活性分别为0.106、0.479和0.495,第一个数据与其他两个有极大差异,说明比表面积大不一定催化活性高,可能还与其他因素有关。
2.3 讨论
催化剂在不进行预还原处理而直接用于甲醇水蒸气重整反应时,在低温条件下CuO物种先启动反应,随后尖晶石逐渐缓释活性铜[24]。反应过程中,活性Cu的释放和烧结长大是同时进行的。由图 5和图 6可知,CuHAl-950催化剂中Cu物种的还原峰温度和最大缓释速率对应的温度都是最低的,CuAAl-950催化剂次之,CuNAl-950催化剂都是最高的。这表明, CuHAl-950催化剂能很快启动反应,催化活性呈上升的趋势;表明此阶段活性Cu的缓释速率大于烧结速率。当尖晶石含量逐渐降低时,活性Cu的烧结速率占主导,催化活性呈逐渐下降的趋势。而CuNAl-950催化剂中的Cu物种都是最难还原的,所以其启动反应的速率慢,而且在整个反应过程中活性Cu的烧结速率一直占主导,因而导致其催化活性非常低。
由图 8可知,CuNAl-950-t催化剂中金属Cu的衍射峰强度最强,CuAAl-950-t次之,CuHAl-950-t最弱,这与表 1中Cu粒子的粒径相对应。根据反应后催化剂的H2-TPR表征,可计算出铜的缓释度(表 1)。比较发现,Cu的大小与缓释度无关,而可能与催化剂的表面结构有关。由图 3可知,CuHAl-950催化剂表面尖晶石结构中含有最多的四配位铜,而CuAAl-950和CuNAl-950催化剂表面尖晶石含更多的六配位铜。由此可以推测,缓释出来的Cu的烧结长大与催化剂表面阳离子配位环境有很大的关系。
总之,由不同铜源制备的铜基催化剂都为尖晶石固溶体,但其比表面积、孔容、孔分布以及表面精细结构(Cu的分布)和还原性能有明显的差异,从而表现出不同的缓释催化行为。
3 结论
三种铜源都可用于合成尖晶石结构的催化剂,且尖晶石的晶粒粒径相差不大,但其含量、比表面积和孔容、表面结构(Cu的分布)以及还原性能有明显的差别,从而导致不同的缓释催化行为。其中, 以氢氧化铜作为铜源合成的催化剂具有良好的催化性能。因此,在原料选取方面,氢氧化铜优于乙酸铜和硝酸铜。
从表征结果可知,不同铜源合成所得催化剂的表面结构(Cu的分布)的细微差别和还原性能的差异是决定缓释催化行为的主要因素。但导致不同铜源合成的催化剂具有不同表面结构和还原性能的具体原因还有待深入研究。
-
-
[1]
李晓峰, 王晶, 张磊, 雷燕秋, 刘攀, 陈然, 陈何臻, 何素芳, 罗永明. 铈和镨改性Ni/Al2O3催化剂对甲醇水蒸气重整制氢的影响[J]. 中国稀土学报, 2016,34,(4): 403-410. LI Xiao-feng, WANG Jing, ZHANG Lei, LEI Yan-qiu, LIU Pan, CHEN Ran, CHEN Ke-zheng, HE Su-fang, LUO Yong-ming. Effect of cerium and praseodymium addition on Ni/Al2O3 catalyst to produce H2 from methanaol steam reforming[J]. J Chin Soc Rare Earths, 2016, 34(4): 403-410.
-
[2]
吝子东, 白松, 张晓辉. 水电解制氢技术发展前景[J]. 舰船防化, 2014(2): 48-54. LIN Zi-dong, BAI Song, ZHANG Xiao-hui. Dexelopment prospect of water electrolysis hydrogen production technology[J]. Chem Defe Ships, 2014, (2): 48-54.
-
[3]
WANG X, GORTE R J. A study of steam reforming of hydrocarbon fuels on Pd/ceria[J]. Appl Catal A:Gen, 2002, 224(1): 209-218.
-
[4]
ILINICH O, RUETTINGER W, LIU X, FARRAUTO R. Cu-Al2O3-CuAl2O4 water-gas shift catalyst for hydrogen production in fuel cell applications:Mechanism of deactivation under start-stop operating conditions[J]. J Catal, 2007, 247(1): 112-118. doi: 10.1016/j.jcat.2007.01.014
-
[5]
RARÓG-PILECKA W, SZMIGIEL D, KOWALCZYK Z, JODZIS S, ZIELINSKI J. Ammonia decomposition over the carbon-based ruthenium catalyst promoted with barium or cesium[J]. J Catal, 2003, 218(2): 465-469. doi: 10.1016/S0021-9517(03)00058-7
-
[6]
王桂芝. 甲醇制氢技术及在燃料电池中的应用[J]. 化学工业, 2008,26,(1): 17-22. WANG Gui-zhi. Technology for production hydrogen from methanol and its application in fuel cell system[J]. Chem Ind, 2008, 26(1): 17-22.
-
[7]
SÁ S, SILVA H, BRANDÃO L, SOUSA J, MENDES A. Catalysts for methanol steam reforming-A review[J]. Appl Catal B:Environ, 2010, 99(1/2): 43-54.
-
[8]
MATSUMURA T, TANAKA K, TODE N, YAZAWA T, HARUTA M. Catalytic methanol decomposition to carbon monoxide and hydrogen over nickel supported on silica[J]. J Mol Catal A:Chem, 2000, 152(1/2): 157-165.
-
[9]
SHEN G, FUJITA S, MATSUMOTO S, TAKEZAWA N. Steam reforming of methanol on binary Cu/ZnO catalysts:Effects of preparation condition upon precursors, surface structure and catalytic activity[J]. J Mol Catal A:Chem, 1997, 124(2): 123-136.
-
[10]
VELU S, SUZUKI K, OSAKI T. Selective production of hydrogen by partial oxidation of methanol over catalysts derived from CuZnAl-layered double hydroxides[J]. Catal lett, 1999, 62(2/4): 159-167. doi: 10.1023/A:1019023811688
-
[11]
VELU S, SUZUKI K. Selective production of hydrogen for fuel cells via oxidative steam reforming of methanol over CuZnAl oxide catalysts:effect of substitution of zirconium and cerium on the catalytic performance[J]. Top Catal, 2003, 22(3/4): 235-244. doi: 10.1023/A:1023576020120
-
[12]
毛丽萍, 吕功煊. 纳米Cu/Al2O3催化剂催化甲醇水蒸气重整制氢研究[J]. 甘肃科学学报, 2009,21,(1): 77-80. MAO Li-ping, LV Gong-xuan. Hydrogen production from methanol steam reforming over nano-Cu/A12O3 catalyst[J]. J Gansu Sci, 2009, 21(1): 77-80.
-
[13]
PURNAMA H, GIRGSDIES F, RESSLER T, SCHATTKA J H, CARUSO R A, SCHOMÄCKER R, SCHLÖGL R. Activity and selectivity of a nanostructured CuO/ZrO2 catalyst in the steam reforming of methanol[J]. Catal Lett, 2004, 94(1/2): 61-68. doi: 10.1023/B:CATL.0000019332.80287.6b
-
[14]
SHISHIDO T, YAMAMOTO Y, MORIOKA H, TAKAKI K, TAKEHIRA K. Active Cu/ZnO and Cu/ZnO/Al2O3 catalysts prepare by homogeneous precipitation method in steam reforming of methanol[J]. Appl Catal A:Gen, 2004, 263(2): 249-253. doi: 10.1016/j.apcata.2003.12.018
-
[15]
OGUCHI H, NISHIGUCHI T, MATSUMOTO T, KANAI H, UTANI K, MATSUMURA Y, IMAMURA S. Steam reforming of methanol over Cu/CeO2/ZrO2 catalysts[J]. Appl Catal A:Gen, 2005, 281(1): 69-73.
-
[16]
KAMEOKA S, TANABE T, TSAI A P. Spinel CuFe2O4:A precursor for copper catalyst with high thermal stability and activity[J]. Catal Lett, 2005, 100(1/2): 89-93.
-
[17]
MAITI S, LLORCA J, DOMINGUEZ M, COLUSSI S, TROVARELLI A, PRIOLKAR K, AQUILANTI G, GAYEN A. Combustion synthesized copper-ion substituted FeAl2O4 (Cu0.1Fe0.9Al2O4):A superior catalyst for methanol steam reforming compared to its impregnated analogue[J]. J Power Sources, 2016, 304: 319-331. doi: 10.1016/j.jpowsour.2015.11.066
-
[18]
YONG S, OOI C, CHAI S, WU X. Review of methanol reforming-Cu-based catalysts, surface reaction mechanisms, and reaction schemes[J]. Int J Hydrogen Energy, 2013, 38(22): 9541-9552. doi: 10.1016/j.ijhydene.2013.03.023
-
[19]
MATSUKATA M, UEMIYA S, KIKUCHI E. Copper-alumina spinel catalysts for steam reforming of methanol[J]. Chem Lett, 1988, 5(5): 761-764.
-
[20]
FUKUNAGA T, RYUMON N, ICHIKUNI N, SHIMAZU S. Characterization of CuMn-spinel catalyst for methanol steam reforming[J]. Catal Commun, 2009, 10(14): 1800-1803. doi: 10.1016/j.catcom.2009.06.001
-
[21]
PUSSANA H, KAJORNSAK F. Cu-Cr, Cu-Mn, and Cu-Fe spinel-oxide-type catalysts for reforming of oxygenated hydrocarbons[J]. J Phys Chem C, 2013, 117(45): 23757-23765. doi: 10.1021/jp407717c
-
[22]
李光俊, 郗宏娟, 张素红, 谷传涛, 庆绍军, 侯晓宁, 高志贤. 尖晶石CuM2O4(M=Al、Fe、Cr)催化甲醇重整反应的特性[J]. 燃料化学学报, 2012,40,(12): 1466-1471. doi: 10.3969/j.issn.0253-2409.2012.12.009LI Guang-jun, XI Hong-juan, ZHANG Su-hong, GU Chuan-tao, QING Shao-jun, HOU Xiao-ning, GAO Zhi-xian. Catalytic characteristics of spinel CuM2O4 (M=Al, Fe, Cr) for the steam reforming of methanol[J]. J Fuel Chem Technol, 2012, 40(12): 1466-1471. doi: 10.3969/j.issn.0253-2409.2012.12.009
-
[23]
HUANG Y H, WANG S F, TSAI A P, KAMEOKA S. Reduction behaviors and catalytic properties for methanol steam reforming of Cu-based spinel compounds CuX2O4 (X=Fe, Mn, Al, La)[J]. Cera Inter, 2014, 40(3): 4541-4551. doi: 10.1016/j.ceramint.2013.08.130
-
[24]
郗宏娟, 李光俊, 庆绍军, 侯晓宁, 赵金珍, 刘雅杰, 高志贤. 固相法合成铜铝尖晶石催化甲醇重整反应[J]. 燃料化学学报, 2013,41,(8): 998-1002. XI Hong-juan, LI Guang-jun, QING Shao-jun, HOU Xiao-ning, ZHAO Jin-zhen, LIU Ya-jie, GAO Zhi-xian. Cu-Al spinel catalyst prepared by solid phase method for methanol steam reforming[J]. J Fuel Chem Technol, 2013, 41(8): 998-1002.
-
[25]
XI H, HOU X, LIU Y, QING S, GAO Z. Cu-Al spinel oxide as an efficient catalyst for methanol steam reforming[J]. Angew Chem, 2014, 53(44): 11886-11889. doi: 10.1002/anie.201405213
-
[26]
GRIONI M, GOEDKOOP J B, SCHOORL R, GROOT F M F, FUGGLR J C, SCHÄFERS F, KOCH E E, ROSSI G, ESTEVA J M, KARNATAK R C. Studies of copper valence states with Cu L3 X-ray-absorption spectroscopy[J]. Phys Rev B, 1989, 39(3): 1541-1545. doi: 10.1103/PhysRevB.39.1541
-
[27]
SHIMIZU K, MAESHIMA H, YOSHIDA H, SATSUMA A, HATTORI T. Spectroscopic characterisation of catalysts for selective Cu-Al2O3 catalytic reduction of NO with propene[J]. Phys Chem Chem Phys, 2000, 2(10): 2435-2439. doi: 10.1039/b000943l
-
[28]
LUO M F, FANG P F, HE M, XIE Y L. In situ XRD, Raman, and TPR studies of CuO/Al2O3 catalysts for CO oxidation[J]. J Mol Catal A:Chem, 2005, 239(1/2): 243-248.
-
[1]
-
表 1 催化剂的特征参数
Table 1. Characteristic parameter of fresh and tested catalysts
Fresh catalyst CuHAl-950 CuAAl-950 CuNAl-950 Cu source Cu(OH)2 Cu(CH3COO)2·H2O Cu(NO3)2·3H2O dspinel/ nm[a] 12.7 12.4 11.3 BET surface area A/ (m2·g-1) 65.9 33.8 25.4 Pore volume v/(cm3·g-1) 0.434 0.213 0.289 X spinel / %[b] 81.3 79.1 93.7 x in Cu1-3xVxAl2+2xO4 0.129 0.134 0.104 After MSR CuHAl-950-t CuAAl-950-t CuNAl-950-t dCu-after MSR / nm[c] 6.6 9.2 20.2 Cu0 surface area A/(m2 ·g-1)[d] 183.9 146.1 94.7 RD/%[e] 88.7 85.9 66.8 [a]: the crystallite size of spinel was calculated by the Scherrer equation with the XRD patterns (Figure 2);
[b]: the molar ratio of Cu in the Cu-Al spinel phase to total Cu as derived from H2-TPR (Figure 5);
[c]: Cu crystalline size of tested catalyst was calculated by the Scherrer equation with XRD patterns (Figure 8);
[d]: Cu surface area of tested catalyst was measured by N2O chemisorption method;
[e]: the releasing degree (RD) of Cu from spinel after catalytic testing was calculated by using H2-TPR data of tested samples -

计量
- PDF下载量: 6
- 文章访问数: 2557
- HTML全文浏览量: 321