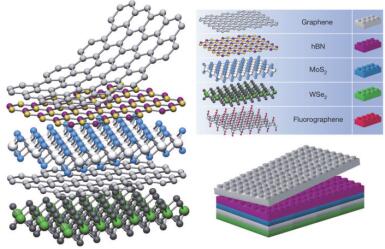

Citation: Tan Xiaoyu, Yang Shaoyan, Li Huijie. Epitaxy of Ⅲ-Nitrides Based on Two-Dimensional Materials[J]. Acta Chimica Sinica, 2017, 75(3): 271-279. doi: 10.6023/A16100552

基于二维材料的Ⅲ族氮化物外延
English
Epitaxy of Ⅲ-Nitrides Based on Two-Dimensional Materials
-
Key words:
- gallium nitride
- / graphene
- / hexagonal boron nitride
- / transition metal dichalcogenides
-
1 引言
Ⅲ族氮化物通常是指氮化铝 (AlN)、氮化镓 (GaN)、氮化铟 (InN) 以及它们所形成的合金 (AlGaN、InGaN、AlInN或AlGaInN).通过调节合金中的组分, AlGaInN的能隙可在0.67~6.2 eV之间连续变化[1], 覆盖了深紫外至近红外的光谱区, 加之其直接带隙的特征, 因此在光电领域有广泛的应用. 2014年诺贝尔物理学奖即授予了天野浩、中村修二、赤崎勇三位科学家, 他们在20世纪90年代前后所做的一系列工作孕育了当前繁荣的LED照明市场.通过调节InGaN的能隙 (0.7~3.4 eV), 有望制备转化效率超过50%的多结太阳能电池[2].同时, AlGaN材料带隙宽 (3.4~6.2 eV)、击穿电压高, 可以制备出性能更高的功率电子器件, 在电力传输和电动汽车领域有望取代当下的Si基功率器件[3]. AlGaN还能通过和GaN形成异质结产生高浓度、高迁移率的二维电子气, 在雷达、通讯领域正逐步取代当前的GaAs基射频器件[4].此外, 由于AlN与GaN晶体具有很强的自发极化和压电系数, 因此在MEMS器件[5, 6]、摩擦电[7]等领域也有很大的应用前景.
目前, 制约Ⅲ族氮化物发展的瓶颈是高质量氮化物材料的低成本制备.不同于Si和GaAs, 由于氮化物的平衡蒸气压很高, 难以通过直拉、浮区熔融等传统方法实现大规模的单晶制备[8].基于当前的制备技术, 如高温高压法、氨热法、钠融法 (Na-flux)、升华法等, 氮化物同质衬底的价格十分昂贵, 且尺寸较小[9].为此, 作为替代的异质外延得到了深入研究.借助分子束外延 (MBE)、金属有机气相外延 (MOCVD)、氢化物气相外延 (HVPE) 等生长技术, 通过低温缓冲层[10, 11]、图形衬底[12]、侧向外延[13]等生长工艺, 人们已实现了氮化物在蓝宝石、碳化硅 (SiC)、硅 (Si) 等异质衬底上较高质量的外延生长, 其结晶质量可以满足当前器件制备的一般需要[14].
但是, 氮化物的进一步发展仍存在诸多问题: (1) 异质外延中的失配问题.由于晶格失配和热胀系数失配[15], 基于蓝宝石、Si的异质外延会在氮化物外延层中产生较大的应力, 产生缺陷甚至裂纹, 影响后续的器件制备; (2) 大功率器件的散热问题.蓝宝石的热导率很低, 大功率工作下温度上升较快会降低氮化物器件的性能; (3) 氮化物器件的薄膜化问题.为了发展可折叠及可穿戴的氮化物器件, 需要把氮化物薄膜器件与柔性衬底结合在一起[16].鉴于柔性衬底难以承受氮化物制备时的高温 (>800 ℃), 因此需要将在蓝宝石、Si上外延的氮化物剥离下来转移至柔性衬底.而不论是基于蓝宝石的激光剥离[17], 或是Si上的化学腐蚀剥离[18], 都需要较高的能耗或时间成本.
二维晶体材料是具有单原子或单分子厚度的层状材料:层内原子间共价键合, 层间则通过微弱的范德瓦尔斯力结合在一起, 如图 1所示[19].继2004年石墨烯的成功剥离与表征后[20], 过渡金属硫族化物 (TMDs, 如MoS2、WSe2等)、六方氮化硼 (h-BN)、黑磷等二维材料相继成为人们的研究热点.维度差异产生的不同于三维体材料的新奇性质, 如石墨烯的高电子迁移率、高热导率、高透光性[21, 22]; 单层MoS2的直接带隙等, 为超级电容器[23, 24]、透明导电膜[25]、晶体管[26, 27]、光探测器[28, 29]、气体传感器[30, 31]、光驱催化[32]等新型微纳器件的研制提供了更多的实现方式.
图 1 二维材料通过范德瓦尔斯力可以形成不同的组合[19] Figure 1. If one considers 2D crystals to be analogous to Lego blocks, the construction of a huge variety of layered structures becomes possible. Reprinted by permission from Macmillan Publishers Ltd: [Nature] (Ref. 19), copyright 2017
二维材料也为氮化物的进一步发展提供了可能: (1) 石墨烯、h-BN、MoS2的高温稳定性使其可耐受氮化物的高温生长条件; (2) 层间弱键合的特性可降低由晶格失配及热胀系数失配产生的应力, 提高材料质量, 并易于实现二维材料的层间分离; (3) 二维材料本身的特性, 如石墨烯的高电导率、热导率, 也会提升氮化物器件的性能.作为氮化物异质外延时的中间层, 相比于低温AlN[11]、多层渐变AlGaN[33]、SiNx[34]、ZnO[35]等体材料, 二维材料具有厚度薄 (几纳米甚至更小)、晶畴尺寸大、层间结合力弱等特点, 有望实现氮化物的高质量外延与转移, 降低氮化物器件对外延衬底的依赖.基于此, 近年来研究者们围绕着二维材料上氮化物的外延制备与转移开展了积极的研究.这些研究包括三方面的内容:
(1) 在传统衬底上实现二维材料的制备; (2) 在二维材料上实现氮化物的制备; (3) 通过二维材料实现氮化物与传统衬底的分离.本文综述了该领域的研究进展, 包括石墨烯、h-BN及TMDs上的氮化物外延.
2 石墨烯上的氮化物外延
石墨烯作为最早被深入研究的二维材料, 其制备方法相对其它二维材料更为成熟.从最早的机械剥离法、氧化石墨还原法, 到SiC热解法、化学气相沉积法 (CVD), 其可控性逐渐增强, 薄膜面积从最初的几十微米[36]发展到如今的30英寸[37], 单晶畴的尺寸也达到了1.5英寸[38].这为研究石墨烯上的氮化物外延提供了良好的材料基础.同时, 石墨烯还具有超高的电导率、热导率和透光性, 使其不但可以作为器件的透明电极[39], 还可以实现器件的高效散热[40].这也是研究者们积极研究石墨烯上氮化物制备的动力.
石墨烯上氮化物外延的关键是氮化物在石墨烯上的成核.理想的石墨烯表面没有成键电子, 外来的原子难以在石墨烯的表面附着并生长成膜.因此, 需要破坏石墨烯的理想表面, 使其在空间上产生悬挂键.研究者们进行的多种尝试可以被归为两类: (1) 在制备石墨烯薄膜时即引入缺陷; (2) 在制备石墨烯薄膜后引入缺陷.以下分别对这两类方法进行介绍.
2.1 制备中引入缺陷
2012年, 韩国蔚山大学的Choi等[41]借助石墨烯表面上的脊实现了GaN薄膜的外延.他们利用扩散辅助合成 (Diffusion Assisted Synthesis, DAS) 的方法[42]在蓝宝石的表面制备石墨烯薄膜.具体做法是首先在室温下的蓝宝石表面沉积一层100 nm的Ni多晶膜, 之后在Ni膜上涂覆碳粉, 在260 ℃下对蓝宝石片施加约1 MPa的压力, 使碳粉中的碳原子通过多晶Ni膜的晶界扩散到蓝宝石的表面并在蓝宝石和Ni膜的界面处形成石墨烯层.这样的石墨烯层会在多晶Ni膜晶界所对应的位置处富集, 形成表面缺陷——脊, 如图 2所示.用FeCl3溶液腐蚀掉Ni膜后, 他们在1040 ℃、通入氮气的条件下对蓝宝石表面进行热退火, 之后在相同温度下利用MOCVD直接进行GaN外延, 得到了GaN薄膜.研究发现, 石墨烯层上的脊作为GaN的成核位点, 提高了GaN在蓝宝石上的浸润能力.同时, 在相同的实验条件下, 当多晶石墨烯层的厚度从0.6 nm增加到7.9 nm时, 外延GaN的生长质量得到了明显改善 (如图 3所示), 表面出现了台阶流模式的生长, 位错密度降低到了1.2×109 cm-2, 略高于传统两步法得到的外延结果 (3×108 cm-2).选区电子衍射 (SEAD) 和隧道电子显微 (TEM) 结果表明, 石墨烯上的氮化镓外延取向与传统的蓝宝石上外延氮化镓时的取向一致.
图 2 碳原子通过Ni晶界向Ni/衬底界面处扩散并形成石墨烯, 由于碳原子的富集使其在晶界处形成“脊”[42] Figure 2. Preferential diffusion of C atoms via GBs in Ni, followed by heterogeneous nucleation at the defect sites and growth via lateral diffusion of C atoms along Ni/substrate interface. Reprinted by permission from Macmillan Publishers Ltd: [Nature Communications] (Ref. 42), copyright 2017
Gupta等[43]利用石墨烯在制备及转移过程中形成的损伤缺陷进行了氮化镓的外延.他们使用CVD在高纯的铜片上以甲烷作为碳源沉积了石墨烯薄膜, 然后用聚甲基丙烯酸甲酯 (PMMA) 涂覆石墨烯表面, 用过硫酸钠溶液腐蚀掉铜片, 转移到热氧化过的Si衬底上后再用丙酮去除PMMA.石墨烯的缺陷包括生长时的晶格缺陷、非刻意引入的有机沾污以及转移中形成的膜层褶皱.借助MOCVD, 外延时他们先生长AlN低温成核层, 然后生长了GaN. Al原子的附着能力较Ga原子更高, 因此更容易在石墨烯表面的缺陷上成核.实验发现, 用GaN作为成核层时, 表面会有零星的GaN大块和含Ga的滴状物; 而用AlN作为成核层时则可使GaN的生长覆盖石墨烯的整个表面. Ⅴ/Ⅲ比值为3500、压强6650 Pa、1000 ℃下, AlN成核层的结晶方向沿[101], 其它方向的生长受到抑制; 当AlN成核层厚度30 nm、外延温度1040 ℃、压强6650 Pa时, 随着原料气中Ⅴ/Ⅲ比值的增大 (500~4500), AlN晶畴的取向逐渐偏向[101].研究者们进而利用该方法在石墨烯上生长了GaN/AlGaN量子阱与InGaN/GaN量子阱[44].尽管量子阱本身是多晶的, 其荧光光谱中的单一发光峰表明量子阱中的组分比较稳定.
Araki等[45]同样借助CVD石墨烯上的缺陷, 用射频MBE技术外延了GaN.他们将铜片上CVD生长的单层多晶石墨烯转移到Si (100) 衬底上, 而后直接外延GaN.外延层厚为400 nm时, 所得的GaN柱状晶畴径向为尺寸0.5~1 μm, (0002) 取向, 彼此间仍有间隙. GaN外延的荧光谱中同时出现了闪锌矿结构的立方相的荧光峰 (3.2 eV) 和纤锌矿结构的六方相的荧光峰 (3.4 eV). TEM成像显示, GaN生长之初在沿着六方相的[0002]方向生长的同时即伴有较多的堆垛层错, 生长几个原子层后转为立方相, 并沿[111]方向生长, 约10 nm后再次转变为六方相并沿[0002]方向生长, 直到生长结束, 如图 3所示.借鉴SiC外延中使用斜切衬底避免层错的出现, 研究者们认为若能在石墨烯的表面形成台阶结构, 则可完全避免层错的出现, 实现GaN的高质量外延.
图 3 GaN/graphene/Si (100) 界面处的高分辨TEM截面图,显示GaN外延过程中晶相发生了多次的转换[45] Figure 3. Cross-sectional high-resolution TEM images of interface region between GaN and graphene/Si (100) substrate. Stacking faults were generated at the initial growth of GaN, which resulted in the cubic phase inclusion. Copyright 2014 The Japan Society of Applied Physics
IBM的Kim等[46]实现了上述想法.他们利用4H-SiC衬底制备了具有台阶结构的石墨烯层, 用MOCVD实现了GaN的高质量外延.在高温 (1575 ℃) 下通入氢气, 4H-SiC表面的Si原子在H2的刻蚀下逃逸表面, 留下的C原子重构形成石墨烯.由于4H-SiC衬底的面法向略微偏离[0002]方向, 因此形成的石墨烯具有原子层级的台阶结构, 台阶的间距随偏离的角度增大而减小, 偏离的角度由SiC衬底抛光时的方向决定.实验中台阶高度5~10 nm, 台阶间距5~10 μm.而后, 使用MOCVD在台阶状的表面外延2.5 μm厚的GaN薄膜.相比于单步法和传统的低温-高温两步法, 采用改进后的两步生长法 (先在1100 ℃下生长GaN成核层; 再在1250 ℃下进行GaN的外延) 可以得到高质量的GaN薄膜, 如图 4所示.当温度高于1250 ℃时, 由于Ga的附着力较低, 无法得到较为明显的GaN外延. GaN的位错密度约为1×109cm-2, 且表现出明显的单晶特征, 与目前主流异质外延所得的结果相近.在此基础上, 通过在GaN的表面沉积一层Ni, 研究者在热释胶的协同下实现了外延GaN膜与石墨烯/SiC衬底的分离, 如图 5所示.拉曼光谱表明, 石墨烯留在了SiC衬底, 而非附着在GaN膜上.且剥离后的GaN表面十分平整, 通过直接接触即可与SiO2/Si衬底稳定结合在一起.同时, 剥离后的石墨烯/SiC衬底可以继续外延GaN薄膜, 且外延的质量依旧很高, 意味着该方法中的SiC衬底可以重复使用.这将大大降低GaN的外延成本.
图 4 (a) 碳化SiC衬底后的石墨烯的AFM成像. (b~d) 外延GaN薄膜的SEM成像, 其中 (b) 传统两步生长法: 580 ℃成核, 1150 ℃生长; (c) 1100 ℃下的一步生长; (d) 改进的两步生长法: 1100 ℃成核, 1150 ℃生长[46] Figure 4. (a) AFM image of the surface of a graphitized SiC substrate. (b~d) Plan-view SEM images of GaN films grown on graphene by (b) the conventional two-step growth (nucleation at 580 ℃ and growth at 1150 ℃), (c) one-step growth at 1100 ℃, and (d) modified two-step growth (nucleation at 1100 ℃ and growth at 1250 ℃). Reprinted by permission from Macmillan Publishers Ltd: [Nature Communications] (Ref. 46), copyright 2014
图 5 利用石墨烯实现单晶薄膜生长/转移的流程. (a) 碳化SiC衬底制备台阶状石墨烯; (b) 外延GaN薄膜; (c) 沉积Ni应力层; (d) 利用胶带实现SiC衬底与GaN薄膜的分离; (e) 将GaN/Ni薄膜转移至目标衬底; (f) 去除Ni层及胶带[46] Figure 5. (a) Graphitization of a SiC substrate to form epitaxy graphene. (b) Epitaxy growth of GaN on graphene. (c) Deposition of a stressor layer (Ni). (d) Release of GaN from the substrate with a handling tape. (e) Transfer of the released GaN/Ni/tape stack on a host substrate. (f) Removal of the tape and Ni by thermal release and wet etching, leaving a GaN film on the host substrate.Reprinted by permission from Macmillan Publishers Ltd: [Nature Communications] (Ref. 46), copyright 2014
韩国全北国立大学的Hong等[47]利用还原氧化石墨烯上的图形缺陷实现了GaN的MOCVD生长.他们在蓝宝石衬底上首先用光刻胶制备圆形柱阵列 (阵列周期4 μm, 圆柱直径2 μm), 接着热喷涂了一层15 nm厚的氧化石墨烯, 然后用丙酮溶解掉了柱状阵列, 露出蓝宝石表面, 形成了圆形孔阵列的氧化石墨烯层, 如图 6所示.之后在1100 ℃下用氢气将氧化石墨烯还原, 形成厚度仅为2 nm圆形孔阵列的石墨烯层, 然后进行GaN的低温-高温两步生长.外延过程中GaN在蓝宝石上成核, 然后通过侧向外延的合并形成GaN薄膜.所得GaN薄膜的位错密度为5.12×108 cm-2.在此基础上制备的InGaN-LED, 其散热得到了明显的改善.相比于直接在蓝宝石上制备的LED, 工作电流100 mA时器件的表面平均温度从51.4 ℃下降到了47.06 ℃.
图 6 制备石墨烯埋层的流程. (a) 通过光刻在蓝宝石衬底上制备圆柱阵列的掩膜图形; (b) 利用喷涂法在衬底上沉积氧化石墨烯; (c) 去除掩膜,得到氧化石墨烯的阵列图形; (d) 热还原衬底得到还原氧化石墨烯,并外延GaN薄膜[47] Figure 6. (a) The formation of circular arrays of photoresist mask on the sapphire substrate by photolithography process. (b) Deposition of graphene oxide on the sapphire substrate by the spray-coating method. (c) Removal of photoresist using acetone (during this step the graphene oxide film with arrays of hole patterns is created). (d) Thermal reduction and direct growth of GaN epilayer structure on the rGO pattern (the hole arrays facilitates the direct growth of GaN). Reprinted by permission from Macmillan Publishers Ltd: [Nature Communications] (Ref. 47), copyright 2014
天津理工大学杨慧等[48]利用氧化还原石墨烯纳米层边缘处的悬挂键尝试了GaN的外延生长.他们在Si (001) 表面上旋涂了带状氧化还原石墨烯片层, 然后通过Ga蒸汽与氨气的反应, 在石墨烯纳米层上生长GaN.由于石墨烯纳米片的尺寸仅为数百纳米, 因此在片层的边缘处的悬挂键成为了GaN的成核位点.生长得到了GaN纳米片.通过控制生长时氨气的比例, 可以得到面取向为[112]的GaN纳米片.
山东大学郝霄鹏等[49]利用旋涂石墨烯上的缺陷实现了GaN的HVPE生长.他们在蓝宝石衬底上先用MOCVD沉积5 μm厚的GaN, 然后将分散在溶剂中的多层石墨烯纳米片旋涂在GaN层的表面, 再置于真空炉中在80 ℃下保持24 h.最后, 利用HVPE在石墨烯表面直接沉积40 μm厚的GaN膜.旋涂的石墨烯纳米片层晶畴间的差异很大, 会形成诸如晶界、层错、褶皱等多种缺陷.对比没有旋涂过石墨烯的MOCVD-GaN/蓝宝石衬底在相同条件下的外延结果, 旋涂石墨烯纳米片层改善了GaN的外延质量, 降低了外延GaN中的应力.由于GaN只在石墨烯的缺陷上成核, 即只与石墨烯的缺陷部分存在强键合, 而与其它区域间的结合力很弱, 因此晶格失配和热胀失配对GaN外延层产生的影响得到了显著的改善.
中科院半导体所李晋闽课题组利用石墨烯上的缺陷生长了高质量的AlN薄膜[50].他们利用常压化学气相沉积 (APCVD) 在蓝宝石衬底上制备了石墨烯后, 利用MOCVD直接生长了AlN薄膜.相比于蓝宝石上的生长, 由于石墨烯表面没有悬挂键, 因此AlN只在石墨烯的缺陷处成核、生长, 其成核密度显著降低 (如图 7所示), 因此其外延质量得到了改善, XRD结果显示其 (0002) 面的半高宽为360 arcsec. TEM图像显示, AlN在石墨烯上的生长初期没有出现类似于GaN的堆垛层错, 这与Al较高的表面附着系数有关.
图 7 AlN/石墨烯/蓝宝石界面处的高分辨TEM图像, 显示了0.7 nm的石墨烯层在1200 ℃的AlN生长后仍保持其晶格结构[50] Figure 7. HRTEM image of the AlN/graphene/sapphire interface shows the presence of an approximately 0.7-nm thick graphene layer keeps its original structure after 1200 ℃ AlN growth. Copyright 2016 The Japan Society of Applied Physics
2.2 制备后引入缺陷
2010年, 首尔国立大学Chung等[16]通过对石墨烯表面进行等离子体处理, 首次实现了氮化物在石墨烯上的外延.如图 8所示, 他们采用机械剥离的方法用胶带从石墨上获得了尺寸介于1 μm~2 mm的石墨烯单层, 而后转移到了蓝宝石 (0002) 衬底表面, 之后用氧等离子体对石墨烯的表面进行轰击, 使其形成缺陷.然后利用MOCVD的方法, 在处理后的石墨烯表面上生长ZnO纳米墙, 最后通过低温-高温 (600 ℃/1100 ℃) 两步法生长了GaN薄膜.研究发现, 没有进行氧等离子体处理时, 尽管石墨烯单层的台阶边缘为GaN提供了成核位点, 但其浓度太低, 只有零星的GaN岛状生长; 氧等离子体处理过的石墨烯上直接外延GaN时, GaN的成核密度提高, 但晶粒的取向随机, 表面粗糙且不规则; 且当作为中间层的ZnO纳米墙的密度较低时, 同样会影响GaN薄膜的生长.只有在ZnO纳米墙的密度较高时, 附于其上生长的GaN才会较快地合并成膜. 600 ℃下生长的低温GaN层用于抑制ZnO纳米墙在后续高温生长环境下的分解, 避免了在GaN外延中引入杂质. TEM分析发现, 低温GaN层与ZnO交界处有较高密度的堆垛层错, 并出现了立方相GaN[51].研究者将铜片上生长的石墨烯转移到了SiO2/Si衬底的表面, 同样对其进行了氧等离子体处理并采用ZnO纳米墙作为中间层, 而后利用低温层-侧向合并层-高温外延层的三步法生长了高质量的GaN薄膜, 实现了非晶表面上的GaN外延[52].进一步的研究表明, ZnO对GaN外延的影响很大.在覆盖有CVD-石墨烯的SiO2/Si衬底上, 不进行任何处理即可生长ZnO纳米线[53].这些ZnO在CVD-石墨烯的晶界上成核.氧等离子处理过的石墨烯表面上缺陷较多, ZnO纳米线的密度也随之增加并连结形成纳米墙.据此, 通过电子束刻蚀的方法即可在石墨烯表面制作出特定的ZnO纳米图形[54].
图 8 利用氧等离子体处理及ZnO纳米墙在石墨烯上制备GaN薄膜. (A) GaN薄膜制备流程图; (B) 氧等离子体处理后的石墨烯薄膜; (C) 石墨烯上的ZnO纳米墙; (D) 外延于ZnO纳米墙上的GaN薄膜[16] Figure 8. (A) Schematic illustrations of fabrication process for epitaxial GaN thin films. (B) Optical microscopic image of oxygen-plasma-treated graphene layers. SEM images of (C) ZnO nanowalls grown on plasma-treated graphene layers and (D) GaN thin film grown on ZnO nanowalls. From [Ref. 16]. Reprinted with permission from AAAS
美国海军实验室Nepal等[55]通过对石墨烯表面进行氟化处理, 实现了GaN在石墨烯上的生长.他们认为, 氧等离子体处理会严重降低石墨烯优异的物理性能, 而作为中间层的ZnO纳米墙则会增加界面的复杂度, 降低最终器件的电学性能.而氟化处理不仅不会降低石墨烯的表面电学性能, 反而能提高表面载流子浓度.他们在4H-SiC表面制备了石墨烯, 然后利用XeF2等离子体脉冲对其表面进行氟化处理, 使石墨烯表面6%~7%的区域形成C-F半离子键, 作为后续的成核位点.由于C-F键能低, 在MBE、MOCVD较高的生长温度下很快断裂, 因此首先采用原子层外延 (ALE) 生长11 nm的AlN成核层, 之后再用MOCVD外延800 nm的GaN薄膜.原子力显微 (AFM) 表明GaN出现了台阶流生长模式, X射线衍射 (XRD) 表明 (2133) 峰摇摆曲线的半高宽为410 arcsec, 说明外延GaN的晶体质量很好.荧光谱中的黄光峰则表明晶体中存在点缺陷.
成均馆大学的Lee等[56]利用臭氧处理石墨烯表面, 实现了GaN的高质量外延.他们将镍基底上生长的石墨烯转移到了SiO2/Si衬底上, 然后在100 ℃下用臭氧气体处理了50个周期, 每个周期均包含3 s的臭氧充气与2 s的氮气排空.最后通过MOCVD的两步生长法制备了GaN.臭氧在石墨烯的表面形成的环氧、羟基等官能团, 为后续的GaN外延提供了成核位点.场发射扫描电子显微 (FESEM) 表明, 转移到SiO2/Si衬底上的石墨烯厚度约有10个原子层, 且3 h的高温 (1040 ℃) 生长后, GaN多晶畴仍旧没能合并成膜, 彼此间存在间隙, 如图 9所示.值得一提的是, 该生长条件下, GaN中的大多数线位错与[0002]的生长方向垂直, KOH热腐蚀后没有观察到腐蚀坑.
图 9 GaN制备流程及相应的FESEM图像. (a) 带有褶皱的石墨烯表面; (b) 530 ℃下生长5 min后形成的GaN初始成核层; (c) 于成核层上在1040 ℃下生长3 h后的GaN晶体[56] Figure 9. (a) As-synthesized graphene surface. White arrows indicate wrinkles. Black arrows indicate bumpy structures that formed during the graphene transfer process. (b) Formation of initial nucleation seeds grown at 530 ℃ for 5 min. (c) GaN crystals grown at 1040 ℃ for 3 h following an initial nucleation step. Reproduced from Ref. 56 with permission of the Royal Society of Chemistry
Heilmann等[57]利用氨气处理石墨烯表面, 实现了取向一致的GaN纳米棒的生长.他们将铜片上生长的石墨烯转移到了蓝宝石衬底上, 然后在1200 ℃及氢气的保护下退火.之后通入氨气, 对石墨烯表面进行10 min的氮化, 而后利用MOCVD分两步生长GaN纳米棒: (1) 在1200 ℃下通入Ⅴ/Ⅲ比为372的原料气体成核, 持续16 s; (2) 在1150 ℃下通入Ⅴ/Ⅲ比为25的原料气体以及少量硅烷, 生长GaN纳米棒. SEM表明, GaN纳米棒既有生长在石墨烯未覆盖的蓝宝石衬底上, 也有生长在石墨烯的晶界或台阶边缘上.荧光光谱表明, 黄光峰出现在GaN纳米棒靠近衬底的位置处, 并且石墨烯上的黄光峰强度高于蓝宝石上的.研究者认为, 是石墨烯晶界处的C原子扩散到了GaN纳米棒中造成了黄光峰, 同时未除净的有机沾污也是黄光峰可能的原因.
全北国立大学Suh等[58]用单壁碳纳米管 (SWCNT) 作为石墨烯上的成核位点生长了GaN.如图 10所示, 他们将铜片上的石墨烯转移到 (0002) 面蓝宝石后, 将分散在十二烷基硫酸钠 (SDS) 水溶液中的SWCNT旋涂在石墨烯表面, 之后利用MOCVD通过两步法生长3 μm厚的GaN薄膜. SWCNT的直径为1.2 nm, 长度2~10 μm, 其无规则的排列为GaN提供了成核位点, AFM表明GaN实现了台阶流的生长模式.相比于直接生长在蓝宝石上的GaN薄膜, SWCNT涂覆的石墨烯衬底降低了外延薄膜中的应力及位错密度 (8.3×108cm-2).进一步制备的InGaN-LED器件表明, 基于石墨烯衬底LED的发光能力较蓝宝石上的有所提高.
图 10 通过SWCNT在石墨烯上生长GaN. (a) 蓝宝石上的石墨烯/碳纳米管复合层 (CGH) 示意图; (b) CGH层上生长的GaN层示意图; (c~e) 蓝宝石上的CGH、CGH上的GaN缓冲层、CGH上的GaN外延层的SEM成像[58] Figure 10. Schematic diagram showing (a) carbon nanotubes and graphene hybrid structure (CGH) on sapphire, and (b) un-doped GaN layer grown on CGH. SEM images of (c) CGH on sapphire, (d) earlier stage of GaN buffer layer formed on CGH, and (e) un-doped GaN layer grown on CGH are shown, respectively. Reprinted with permission from the author (Eun Kyung-Suh)
佐治亚理工学院Ougazzaden等[59]通过反应离子刻蚀在石墨烯上作出了成核位点.他们首先在4H-SiC衬底上高温制备了5~8个原子层厚的石墨烯层, 之后通过光刻与反应离子刻蚀在石墨烯上作出了圆孔阵列图案, 孔的直径为75 nm, 并露出石墨烯下的4H-SiC表面.而后通过MOCVD沉积了30 nm的GaN.研究表明, 在5~8层厚的石墨烯掩膜下, GaN首先在SiC的表面成核, 形成立方相结构并沿[111]方向生长; 当越过石墨烯边界时, 开始沿径向生长.随着生长的进行, 由立方相转变为六方相, 如图 11所示.
图 11 外延在石墨烯孔边沿处的GaN纳米台的STEM成像, 显示了界面处立方相和六方相的交错[59] Figure 11. (a) Cross-sectional STEM image; Zoom and definition of (b) wurtzite zone and (c) cubic zone; FFT diffraction pattern of the area in the green box showing (b') wurtzite GaN and (c') c-GaN, where (110) faces the reader; local intensity maxima (111) and (111) make an angle of 70.5° relative to the origin, characteristic of the zinc-blende/cubic lattice. (d) STEM analysis and crystallographic directions. (e) Interface in the vicinity of the EG mask, showing both cubic and wurtzite phases on GaN, as well as the biphasic transition region. Reprinted from [Ref. 59], with the permission of AIP Publishing
3 h-BN上的氮化物外延
由于h-BN既是二维材料, 也是氮化物, 因此对于GaN或AlN的外延具有一定的优势. h-BN的制备方法包括机械剥离[60]、低压化学气相沉积 (LPCVD)[61]、MOCVD[62]、离子束溅射沉积 (ISBD)[63]等.目前, 半导体所的张兴旺课题组通过ISBD[63]制备了尺寸超过100 μm的h-BN单晶膜, 厦门大学的蔡端俊等则实现了7英寸h-BN薄膜的LPCVD生长和转移[61].这使研究h-BN上的氮化物外延具有了实际意义.
2012年, 日本NTT实验室Kobayashi等[62]在h-BN上成功实现了GaN-LED的外延生长与剥离.如图 12所示, 他们通过MOCVD在蓝宝石衬底上外延生长了3 nm的h-BN, 然后借助100 nm厚的AlN缓冲层外延了高质量的GaN薄膜, 其位错密度为8.6×109cm-2.之后, 在GaN薄膜上外延了InGaN LED, 并用热释胶成功实现了LED与衬底的分离.研究表明, 直接在h-BN上外延GaN时得到的是多晶膜, 需要AlN或AlGaN作为缓冲层才能够得到高质量的单晶.剥离时, 分离发生在h-BN层的N原子和B原子之间.拉曼谱表明, 相对于剥离前, GaN薄膜中的应力在剥离后得到了释放.研究者研究了转移工艺, 实现了2英寸InGaN/GaN量子阱的完整剥离[64].进一步, 他们利用Au-Ti/Au在加热加压下的键合, 改善了GaN薄膜与被转移衬底界面间的热学及电学接触, 增强了GaN基HEMT器件的散热能力, 提高了输出功率[65].
图 12 MQW材料设计、转移流程图. (a) 在蓝宝石上生长单晶h-BN层后, 生长AlGaN缓冲层及MQW结构; (b) 将MQW结构倒置并与另一衬底通过In层叠在一起; (c) 热处理增强In层的结合性; (d) 通过机械方法剥离蓝宝石衬底, 完成MQW结构与外来衬底的结合[62] Figure 12. (a) Single-crystal h-BN release layer growth is performed on a sapphire substrate, followed by growth of wurtzite AlGaN layer and the MQW structure. (b) The MQW structure is flipped upside down and placed on a foreign substrate via an adhesive indium sheet. (c) Heat-sealing of the indium, and then (d) the MQW structure is released from the host sapphire substrate by mechanical force and transferred to the foreign substrate. Reprinted by permission from Macmillan Publishers Ltd: [Nature] (Ref. 62), copyright 2012
山东大学郝霄鹏等[49]用旋涂h-BN的方法同样实现了GaN的外延生长.他们利用MOCVD在蓝宝石的表面外延了5 μm的GaN薄膜, 之后将分散在溶剂里的h-BN纳米片旋涂在其表面, 接着通过HVPE生长了40 μm的GaN薄膜.对比相同条件下直接在MOCVD-GaN/蓝宝石衬底上生长的GaN, 旋涂了h-BN的样品具有更小的半高宽和位错密度, GaN薄膜的质量得到了提高.研究者认为, h-BN纳米片阻挡了MOCVD-GaN中的线位错向HVPE-GaN的进一步传播, 因此提升了HVPE-GaN的晶体质量.
4 TMDs上的氮化物外延
过渡金属硫族化物 (TMDs) 是二维材料中的一大类, 其中的MoS2、WS2、MoSe2、WSe2等由于其优异的光电性质得到了较为广泛的研究[29]. TMDs所形成的二维晶体类似三明治结构, 上下两层硫族原子 (S, Se等) 夹着中间的一层金属 (Mo、W、Ta、Nb等) 原子.其中, MoS2与WS2的晶格常数与GaN的晶格常数非常接近, 且均为六重对称性, 因此在氮化物外延方面受到一定的关注.早在1999年, 筑波大学Akimoto等[66, 67]利用MoS2作为衬底, 通过MBE的方法在其上外延了GaN, XRD结果显示其 (0002) 晶面的半高宽仅为190 arcsec.不过, 他们使用的衬底为块状MoS2材料, 厚度通常在几百微米, 而非几个原子层厚的二维材料.
2016年Gupta等[68]报道了TMDs上GaN的制备.受限于TMDs尚不成熟的制备技术, 他们使用的MoS2、WS2单晶畴尺寸仅为十几微米.借助MOCVD, 通过低温/高温 (900 ℃/1040 ℃) 两步法, 他们实现了GaN在TMDs/SiO2/Si衬底上的外延.研究表明, H2会与S反应生成H2S气体从而破坏MoS2、WS2的表面结构, 因此需用N2作为有机源的载气.由于高温下氨气也会产生出一定量的H2, 在GaN高温生长阶段, MoS2会发生分解, S原子逸出而Mo原子留下, 如图 13所示.对比直接在Mo原子层上外延时所得的取向杂乱的GaN晶柱, 研究者认为尽管MoS2在GaN的高温生长阶段发生了分解, 却通过影响GaN初始阶段的成核状况实现了GaN在衬底表面的保形生长, 改善了GaN的晶体质量.
图 13 MoS2对GaN生长的作用. SEM图像显示 (a) MoS2上生长的GaN; (b) Mo金属上外延生长的GaN[68] Figure 13. Necessity of MoS2 for GaN growth. (a) Hexagonal crystals of GaN obtained on MoS2 flakes; (b) Faceted chunks of GaN on Mo substrates. Reprinted with permission from the author (Arnab Bhattacharya)
5 结论与展望
发展二维材料上的氮化物制备技术有助于降低氮化物器件的成本, 并实现氮化物器件的高质量、薄膜化制备, 从而将其应用拓展至可穿戴电子领域.本文介绍了研究者们运用MOCVD、MBE、ALD等方法, 借助材料自身的缺陷, 或者刻意引入新的缺陷, 在石墨烯、h-BN、MoS2等二维材料上制备氮化物的一系列工作.归纳这些工作可以得出二维材料上的氮化物外延具有如下特点: (1) 二维材料层间弱键合的特性确实降低了氮化物外延层中的应力.尤其是当外延层的厚度仅为数百纳米、排除了外延层厚度对其应力改善的因素时, 该结论更加明显; (2) 氮化物在二维材料上的生长过程均符合如下演进模式:岛状生长>>侧向外延>>合并成膜>>二维生长.其中, 二维材料上的缺陷决定了岛的密度和分布, 氮化物的生长条件 (如温度、Ⅴ/Ⅲ比、掺杂元素等) 则决定了侧向外延的过程, 二者共同决定了外延层合并成膜时的“合并厚度”及晶体的生长质量; (3) GaN在各种二维材料上外延的初期均存在立方相和六方相交替的现象, 该过程对后续的晶体生长有一定影响; (4) 尽管二维材料与氮化物之间是弱键合, 但在晶格匹配时, 仍能改善氮化物的生长质量.
目前, 基于SiC外延石墨烯和MOCVD外延h-BN上的氮化物制备均实现了器件的胶带式剥离.受益于二者较为成熟的大面积制备技术, 可以预计其商业化即将到来.而MoS2则还未实现外延氮化物的剥离, 其进一步的发展依赖于MoS2大面积制备技术的突破[69].但其与氮化镓之间匹配的晶格参数, 以及优异的光学性质则有望与氮化物构成新型器件.我们相信随着逐渐实现对成核位点的精细调控, 以及对氮化物侧向外延过程的深入了解, 二维材料上的氮化物质量将取得进一步的提升, 基于氮化物的低功耗薄膜器件将会因此而得到极大的发展, 为氮化物器件在照明、通讯、能源、健康等领域的广泛应用奠定基础.
-
-
[1]
Moram, M. A.; Vickers, M. E. Rep. Prog. Phys. 2009, 72, 036502. doi: 10.1088/0034-4885/72/3/036502
-
[2]
Wu, J.; Walukiewicz, W.; Yu, K. M.; Ager Ⅲ, J. W.; Haller, E. E.; Lu, H.; William, J. S.; Metzger, W. K.; Sarah, K. J. Appl. Phys.2003, 94, 6477. doi: 10.1063/1.1618353
-
[3]
Flack, T. J.; Pushpakaran, B. N.; Bayne, S. B. J. Electron. Ma-ter.2016, 45, 2673. doi: 10.1007/s11664-016-4435-3
-
[4]
Florian, C.; Cignani, R.; Santarelli, A.; Filicori, F.; Longo, F. In IEEE MTT-S International Microwave Symposium Digest, IEEE, New York, 2013.
-
[5]
Cimalla, V.; Pezoldt, J.; Ambacher, O. J. Phys. D:Appl. Phys. 2007, 40, 6386. doi: 10.1088/0022-3727/40/20/S19
-
[6]
Hou, Y. H.; Zhang, M.; Han, G. W.; Si, C. W.; Zhao, Y. M.; Ning, J. J. Semicod. 2016, 37, 101001. doi: 10.1088/1674-4926/37/10/101001
-
[7]
Zhao, Z. F. Ph. D. Dissertation, University of Chinese Academy of Sciences, Beijing, 2016.
-
[8]
Wu, Y. F.; Guerrero, J.; McKay, J.; Smith, K. In IEEE Workshop on Wide Bandgap Power Devices and Applications (WiPDA), IEEE, New York, 2014, pp. 30~32, 13~15.
-
[9]
Avrutin, V.; Silversmith, D. J.; Mori, Y.; Kawamura, F.; Kitaoka, Y.; Morkoc, H. Proc. IEEE. 2010, 98, 1302. doi: 10.1109/JPROC.2010.2044967
-
[10]
Amano, H.; Sawaki, N.; Akasaki, I.; Toyoda, Y. Appl. Phys. Lett. 1986, 48, 353. doi: 10.1063/1.96549
-
[11]
Nakamura, S. Jpn. J. Appl. Phys., Part 21991, 30, L1705. doi: 10.1143/JJAP.30.L1705
-
[12]
Cui, L.; Wang, G. G.; Zhang, H. Y.; Zhou, F. Q.; Han, J. C. J. Inorg. Mater. 2012, 27, 897. doi: 10.3724/SP.J.1077.2012.11785
-
[13]
Kato, Y.; Kitamura, S.; Hiramatsu, K.; Sawaki, N. J. Cryst. Growth.1994, 144, 133. doi: 10.1016/0022-0248(94)90448-0
-
[14]
Narukawa, Y.; Ichikawa, M.; Sanga, D.; Sano, M.; Mukai, T. J. Phys. D:Appl. Phys. 2010, 43, 354002. doi: 10.1088/0022-3727/43/35/354002
-
[15]
Wong, Y. Y.; Chiu, Y. S.; Luong, T. T.; Lin, T. M.; Ho, Y. T.; Lin, Y. C.; Chang, E. Y. In Growth and Fabrication of AlGaN/GaN HEMT on SiC Substrate, 10th IEEE International Conference on Semiconductor Electronics, IEEE, New York, 2012, pp. 729~732.
-
[16]
Chung, K.; Lee, C. H.; Yi, G. C. Science, 2010, 330, 655. doi: 10.1126/science.1195403
-
[17]
Wong, W. S.; Sands, T.; Cheung, N. W. Appl. Phys. Lett. 1998, 72, 599. doi: 10.1063/1.120816
-
[18]
Zang, K. Y.; Cheong, D. W. C.; Liu, H. F.; Liu, H.; Teng, J. H.; Chua, S. J. Nanoscale Res. Lett. 2010, 5, 1051. doi: 10.1007/s11671-010-9601-6
-
[19]
Geim, A. K.; Grigorieva, I. V. Nature 2013, 499, 419. doi: 10.1038/nature12385
-
[20]
Novoselov, K. S.; Geim, A. K.; Morozov, S. V.; Jiang, D.; Zhang, Y.; Dubonos, S. V.; Grigorieva, I. V.; Firsov, A. A. Science 2004, 306, 666. doi: 10.1126/science.1102896
-
[21]
Geim, A. K.; Novoselov, K. S. Nat. Mater 2007, 6, 183. doi: 10.1038/nmat1849
-
[22]
林源为, 郭雪峰, 化学学报, 2014, 72, 277. doi: 10.6023/A13080908Lin, Y. W.; Guo, X. F. Acta Chim. Sinica 2014, 72, 277(in Chinese). doi: 10.6023/A13080908
-
[23]
Hu, H. X.; Hu, Z. G.; Ren, X. Y.; Yang, Y. Y.; Qiang, R. B.; An, N.; Wu, H. Y. Chin. J. Chem. 2015, 33, 199. doi: 10.1002/cjoc.v33.2
-
[24]
Jiang, S. Z.; , Qiu, H. W.; Gao, S. S.; Chen, P. X.; Li, Z.; Yu, K. Y.; Yue, W. W.; Yang, C.; Huo, Y. Y.; Wang, S. Y. Chin. J. Chem. 2016, 34, 1039. doi: 10.1002/cjoc.v34.10
-
[25]
Kim, K. S.; Zhao, Y.; Jang, H.; Lee, S. Y.; Kim, J. M.; Kim, K. S.; Ahn, J. H.; Kim, P.; Choi, J. Y.; Hong, B. H. Nature 2009, 457, 706. doi: 10.1038/nature07719
-
[26]
Radisavljevic, B.; Radenovic, A.; Brivio, J.; Giacometti, V.; Kis, A. Nat. Nanotechnol. 2011, 6, 147. doi: 10.1038/nnano.2010.279
-
[27]
何学侠, 刘富才, 曾庆圣, 刘政, 化学学报, 2015, 73, 924. doi: 10.6023/A15040280He, X. X.; Liu, F. C.; Zeng, Q. S.; Liu, Z. Acta Chim. Sinica 2015, 73, 924(in Chinese). doi: 10.6023/A15040280
-
[28]
Lopez-Sanchez, O.; Lembke, D.; Kayci, M.; Radenovic, A.; Kis, A. Nat. Nanotechnol. 2013, 8, 497. doi: 10.1038/nnano.2013.100
-
[29]
Lou, Z.; Liang, Z. Z.; Shen, G. Z. J. Semicond. 2016, 37, 091001. doi: 10.1088/1674-4926/37/9/091001
-
[30]
Schedin, F.; Geim, A. K.; Morozov, S. V.; Hill, E. W.; Blake, P.; Katsnelson, M. I.; Novoselov, K. S. Nat. Mater. 2007, 6, 652. doi: 10.1038/nmat1967
-
[31]
Jiang, S. Z.; , Qiu, H. W.; Gao, S. S.; Chen, P. X.; Li, Z.; Yu, K. Y.; Yue, W. W.; Yang, C.; Huo, Y. Y.; Wang, S. Y. Chin. J. Chem. 2016, 34, 1039. doi: 10.1002/cjoc.v34.10
-
[32]
Li, Y. G.; Wang, H. L.; Xie, L. M.; Liang, Y. Y.; Hong, G. S.; Dai, H. J. J. Am. Chem. Soc. 2011, 133, 7296. doi: 10.1021/ja201269b
-
[33]
Cheng, K.; Leys, M.; Degroote, S.; Daele, B. V.; Boeykens, S.; Derluyn, J.; Germain, M.; Tendeloo, G. V.; Engelen, J.; Borghs, G. J. Electron. Mater. 2006, 35, 592. doi: 10.1007/s11664-006-0105-1
-
[34]
Lahreche, H.; Vennegues, P.; Beaumont, B.; Gibart, P. J. Cryst. Growth 1999, 205, 245. doi: 10.1016/S0022-0248(99)00299-7
-
[35]
Ueda, T.; Huang, T. F.; Sprutte, S.; Lee, H.; Yuri, M.; Itoh, K.; Baba, T.; Harris, J. S. J. Cryst. Growth, 1998, 187, 340. doi: 10.1016/S0022-0248(97)00886-5
-
[36]
Zhang, Y. B.; Tan, Y. W.; Stormer, H. L.; Kim, P. Nature 2005, 438, 201. doi: 10.1038/nature04235
-
[37]
Bae, S. K.; Kim, H. K.; Lee, Y. B.; Xu, X. F.; Park, J. S.; Zheng, Y.; Balakrishnan, J.; Tian, L.; Kim, H. R.; Song, Y. Ⅱ; Kim, Y. J.; Kim, K. S.; Ozyilmaz, B.; Ahn, J. H.; Hong, B. H.; Iijima, S. Nat. Nanotechnol. 2010, 5, 574. doi: 10.1038/nnano.2010.132
-
[38]
Wu, T. R.; Zhang, X. F.; Yuan, Q. H.; Xue, J. C.; Lu, G. Y.; Liu, Z. H.; Wang, H. S.; Wang, H. M.; Ding, F.; Yu, Q. K.; Xie, X. M.; Jiang, M. H. Nat. Mater. 2016, 15, 43.
-
[39]
Rana, K.; Singh, J.; Ahn, J. H. J. Mater. Chem. C 2014, 2, 2646. doi: 10.1039/c3tc32264e
-
[40]
Hiroki, M.; Kumakura, K.; Kobayashi, Y.; Akasaka, T.; Makimoto, T.; Yamamoto, H. Appl, Phys. Lett. 2014, 105, 193509. doi: 10.1063/1.4901938
-
[41]
Choi, J. K.; Huh, J. H.; Kim, S. D.; Moon, D.; Yoon, D.; Joo, K.; Kwak, J.; Chu, J. H.; Kim, S. Y.; Park, K.; Kim, Y. W.; Yoon, E.; Cheong, H.; Kwon, S. Y. Nanotechnology 2012, 43, 435603.
-
[42]
Kwak, J.; Chu, J. H.; Choi, J. K.; Park, S. D.; Go, H.; Kim, S. Y.; Park, K.; Kim, S. D.; Kim, Y. W.; Yoon, E.; Kodambaka, S.; Kwon, S. Y. Nat. Commun. 2012, 3, 645. doi: 10.1038/ncomms1650
-
[43]
Gupta, P.; Rahman, A. A.; Hatui, N.; Gokhale, M. R.; Deshmukh, M. M.; Bhattacharya, A. J. Cryst. Growth 2013, 372, 105. doi: 10.1016/j.jcrysgro.2013.03.020
-
[44]
Gupta, P.; Rahman, A. A.; Hatui, N.; Parmar, J. B.; Chalke, B. A.; Bapat, R. D.; Purandare, S. C.; Deshmukh, M. M.; Bhattacharya, A. Appl. Phys. Lett. 2013, 103, 181108. doi: 10.1063/1.4827539
-
[45]
Araki, T.; Uchimura, S.; Sakaguchi, J.; Nanishi, Y.; Fujishima, T.; Hsu, A.; Kim, K. K.; Palacios, T.; Pesquera, A.; Centeno, A.; Zurutuza, A. Appl. Phys. Express 2014, 7, 071001. doi: 10.7567/APEX.7.071001
-
[46]
Kim, J.; Bayram, C.; Park, H.; Cheng, C. W.; Dimitrakopoulos, C.; Ott, J. A.; Reuter, K. B.; Bedell, S. W.; Sadana, D. K. Nat. Commun. 2014, 5, 4836. doi: 10.1038/ncomms5836
-
[47]
Han, N.; Cuong, T. V.; Han, M.; Ryu, B. D.; Chandramohan, S.; Park, J. B.; Kang, J. H.; Park, Y. J.; Ko, K. B.; Kim, H. Y.; Kim, H. K.; Ryu, J. H.; Katharria, Y. S.; Choi, C. J.; Hong, C. H. Nat. Commun.2013, 4, 1452. doi: 10.1038/ncomms2448
-
[48]
Yang, H.; Li, J. L.; Jia, R. F.; Yang, L. L.; Li, L. RSC Adv. 2016, 6, 43874. doi: 10.1039/C6RA02440H
-
[49]
Zhang, L.; Li, X. L.; Shao, Y. L.; Yu, J. X.; Hao, X. P.; Yin, Z. M.; Dai, Y. B.; Tian, Y.; Huo, Q.; Shen, Y. N.; Hua, Z.; Zhang, B. G. ACS Appl. Mater. Interfaces 2015, 7, 4504. doi: 10.1021/am5087775
-
[50]
Zeng, Q.; Chen, Z. L.; Zhao, Y.; Wei, T. B.; Chen, X.; Zhang, Y.; Yuan, G. D.; Li, J. M. Jpn. J. Appl. Phys. 2016, 55, 085501. doi: 10.7567/JJAP.55.085501
-
[51]
Yoo, H.; Chung, K.; Choi, Y. S.; Kang, C. S.; Oh, K. H.; Kim, M.; Yi, G. C. Adv. Mater. 2012, 24, 515. doi: 10.1002/adma.201103829
-
[52]
Chung, K.; Park, S. I.; Baek, H.; Chung, J. S.; Yi, G. C. Npg Asia Mater. 2012, 4, e24.
-
[53]
Baek, H.; Lee, C. H.; Chung, K.; Yi, G. C. Nano Lett. 2013, 13, 2782. doi: 10.1021/nl401011x
-
[54]
Kim, Y. J.; Yoo, H.; Lee, C. H.; Park, J. B.; Baek, H.; Kim, M.; Yi, G. C. Adv. Mater. 2012, 24, 5565. doi: 10.1002/adma.201201966
-
[55]
Nepal, N.; Wheeler, V. D.; Anderson, T. J.; Kub, F. J.; Masro, M. A.; Myers-Ward, R. L.; Qadri, S. B.; Freitas, J. A.; Hernandes, S. C.; Nyakiti, L. O.; Walton, S. G.; Gaskill, K.; Eddv, C. R. Appl. Phys. Express 2013, 6, 061003. doi: 10.7567/APEX.6.061003
-
[56]
Chae, S. J.; Kim, Y. H.; Seo, T. H.; Duong, D. L.; Lee, S. M.; Park, M. H.; Kim, E. S.; Bae, J. J.; Lee, S. Y.; Jeong, H.; Suh, E. K.; Yang, C. W.; Jeong, M. S.; Lee, Y. H. RSC Adv. 2015, 5, 1343. doi: 10.1039/C4RA12557F
-
[57]
Heilmann, M.; Sarau, G.; Gobelt, M.; Latzel, M.; Sadhujan, S.; Tessarek, C.; Christiansen, S. Cryst. Growth Des. 2015, 15, 2079. doi: 10.1021/cg5015219
-
[58]
Seo, T. H.; Park, A. H.; Park, S.; Kim, Y. H.; Lee, G. H.; Kim, M. J.; Jeong, M. S.; Lee, Y. H.; Hahn, Y. B.; Suh, E. K. Sci. Rep. 2015, 5, 7747. doi: 10.1038/srep07747
-
[59]
Puybaret, R.; Patriarche, G.; Jordan, M. B.; Sundaram, S.; El Gmili, Y.; Salvestrini, J. P.; Voss, P. L.; de Heer, W. A.; Berger, C.; Ougazzaden, A. Appl. Phys. Lett. 2015, 108, 103105.
-
[60]
Pacile, D.; Meyer, J. C.; Girit, C. O.; Zettl, A. Appl. Phys. Lett. 2008, 92, 133107. doi: 10.1063/1.2903702
-
[61]
Wu, C. P.; Soomro, A. M.; Sun, F. P.; Wang, H. C.; Liu, C.; Yang, X. D.; Kang, J. Y.; Cai, D. J. Phys. Status Solidi B 2016, 253, 829. doi: 10.1002/pssb.201552619
-
[62]
Kobayashi, Y.; Kumakura, K.; Akasaka, T.; Makimoto, T. Nature, 2012, 484, 223. doi: 10.1038/nature10970
-
[63]
Wang, H.; Zhang, X.; Liu, H.; Yin, Z.; Meng, J.; Xia, J.; Meng, X. M.; Wu, J.; You, J. Adv. Mater. 2015, 27, 8109. doi: 10.1002/adma.201504042
-
[64]
Ayari, T.; Sundaram, S.; Li, X.; El Gmili, Y.; Voss, P. L.; Sal-vestrini, J. P.; Ougazzaden, A. Appl. Phys. Lett. 2016, 108, 171106. doi: 10.1063/1.4948260
-
[65]
Hiroki, M.; Kumakura, K.; Yamamoto, H. Jpn. J. Appl. Phys. 2016, 55, 05FH07.
-
[66]
Yamada, A.; Ho, K. P.; Maruyama, T.; Akimoto, K. Appl. Phys. A:Mater. Sci. & Process 1999, 69, 89.
-
[67]
Yamada, A.; Ho, K. P.; Akaogi, T.; Maruyama, T.; Akimoto, K. J. Cryst. Growth 1999, 201, 332.
-
[68]
Gupta, P.; Rahman, A. A.; Subramanian, S.; Gupta, S.; Tham-izhavel, A.; Orlova, T.; Rouvimov, S.; Protasenko, V.; Laskar, M. R.; Xing, H. G.; Jena, D.; Bhattacharya, A. Sci. Rep. 2016, 6, 23708. doi: 10.1038/srep23708
-
[69]
许冠辰, 卢至行, 张琪, 邱海龙, 焦丽颖, 化学学报, 2015, 73, 895. doi: 10.6023/A15030203Xu, G. C.; Lu, Z. X.; Zhang, Q.; Qiu, H. L.; Jiao, L. Y. Acta Chim. Sinica 2015, 73, 895(in Chinese). doi: 10.6023/A15030203
-
[1]
-
图 2 碳原子通过Ni晶界向Ni/衬底界面处扩散并形成石墨烯, 由于碳原子的富集使其在晶界处形成“脊”[42]
Figure 2 Preferential diffusion of C atoms via GBs in Ni, followed by heterogeneous nucleation at the defect sites and growth via lateral diffusion of C atoms along Ni/substrate interface. Reprinted by permission from Macmillan Publishers Ltd: [Nature Communications] (Ref. 42), copyright 2017
图 3 GaN/graphene/Si (100) 界面处的高分辨TEM截面图,显示GaN外延过程中晶相发生了多次的转换[45]
Figure 3 Cross-sectional high-resolution TEM images of interface region between GaN and graphene/Si (100) substrate. Stacking faults were generated at the initial growth of GaN, which resulted in the cubic phase inclusion. Copyright 2014 The Japan Society of Applied Physics
图 4 (a) 碳化SiC衬底后的石墨烯的AFM成像. (b~d) 外延GaN薄膜的SEM成像, 其中 (b) 传统两步生长法: 580 ℃成核, 1150 ℃生长; (c) 1100 ℃下的一步生长; (d) 改进的两步生长法: 1100 ℃成核, 1150 ℃生长[46]
Figure 4 (a) AFM image of the surface of a graphitized SiC substrate. (b~d) Plan-view SEM images of GaN films grown on graphene by (b) the conventional two-step growth (nucleation at 580 ℃ and growth at 1150 ℃), (c) one-step growth at 1100 ℃, and (d) modified two-step growth (nucleation at 1100 ℃ and growth at 1250 ℃). Reprinted by permission from Macmillan Publishers Ltd: [Nature Communications] (Ref. 46), copyright 2014
图 5 利用石墨烯实现单晶薄膜生长/转移的流程. (a) 碳化SiC衬底制备台阶状石墨烯; (b) 外延GaN薄膜; (c) 沉积Ni应力层; (d) 利用胶带实现SiC衬底与GaN薄膜的分离; (e) 将GaN/Ni薄膜转移至目标衬底; (f) 去除Ni层及胶带[46]
Figure 5 (a) Graphitization of a SiC substrate to form epitaxy graphene. (b) Epitaxy growth of GaN on graphene. (c) Deposition of a stressor layer (Ni). (d) Release of GaN from the substrate with a handling tape. (e) Transfer of the released GaN/Ni/tape stack on a host substrate. (f) Removal of the tape and Ni by thermal release and wet etching, leaving a GaN film on the host substrate.Reprinted by permission from Macmillan Publishers Ltd: [Nature Communications] (Ref. 46), copyright 2014
图 6 制备石墨烯埋层的流程. (a) 通过光刻在蓝宝石衬底上制备圆柱阵列的掩膜图形; (b) 利用喷涂法在衬底上沉积氧化石墨烯; (c) 去除掩膜,得到氧化石墨烯的阵列图形; (d) 热还原衬底得到还原氧化石墨烯,并外延GaN薄膜[47]
Figure 6 (a) The formation of circular arrays of photoresist mask on the sapphire substrate by photolithography process. (b) Deposition of graphene oxide on the sapphire substrate by the spray-coating method. (c) Removal of photoresist using acetone (during this step the graphene oxide film with arrays of hole patterns is created). (d) Thermal reduction and direct growth of GaN epilayer structure on the rGO pattern (the hole arrays facilitates the direct growth of GaN). Reprinted by permission from Macmillan Publishers Ltd: [Nature Communications] (Ref. 47), copyright 2014
图 7 AlN/石墨烯/蓝宝石界面处的高分辨TEM图像, 显示了0.7 nm的石墨烯层在1200 ℃的AlN生长后仍保持其晶格结构[50]
Figure 7 HRTEM image of the AlN/graphene/sapphire interface shows the presence of an approximately 0.7-nm thick graphene layer keeps its original structure after 1200 ℃ AlN growth. Copyright 2016 The Japan Society of Applied Physics
图 8 利用氧等离子体处理及ZnO纳米墙在石墨烯上制备GaN薄膜. (A) GaN薄膜制备流程图; (B) 氧等离子体处理后的石墨烯薄膜; (C) 石墨烯上的ZnO纳米墙; (D) 外延于ZnO纳米墙上的GaN薄膜[16]
Figure 8 (A) Schematic illustrations of fabrication process for epitaxial GaN thin films. (B) Optical microscopic image of oxygen-plasma-treated graphene layers. SEM images of (C) ZnO nanowalls grown on plasma-treated graphene layers and (D) GaN thin film grown on ZnO nanowalls. From [Ref. 16]. Reprinted with permission from AAAS
图 9 GaN制备流程及相应的FESEM图像. (a) 带有褶皱的石墨烯表面; (b) 530 ℃下生长5 min后形成的GaN初始成核层; (c) 于成核层上在1040 ℃下生长3 h后的GaN晶体[56]
Figure 9 (a) As-synthesized graphene surface. White arrows indicate wrinkles. Black arrows indicate bumpy structures that formed during the graphene transfer process. (b) Formation of initial nucleation seeds grown at 530 ℃ for 5 min. (c) GaN crystals grown at 1040 ℃ for 3 h following an initial nucleation step. Reproduced from Ref. 56 with permission of the Royal Society of Chemistry
图 10 通过SWCNT在石墨烯上生长GaN. (a) 蓝宝石上的石墨烯/碳纳米管复合层 (CGH) 示意图; (b) CGH层上生长的GaN层示意图; (c~e) 蓝宝石上的CGH、CGH上的GaN缓冲层、CGH上的GaN外延层的SEM成像[58]
Figure 10 Schematic diagram showing (a) carbon nanotubes and graphene hybrid structure (CGH) on sapphire, and (b) un-doped GaN layer grown on CGH. SEM images of (c) CGH on sapphire, (d) earlier stage of GaN buffer layer formed on CGH, and (e) un-doped GaN layer grown on CGH are shown, respectively. Reprinted with permission from the author (Eun Kyung-Suh)
图 11 外延在石墨烯孔边沿处的GaN纳米台的STEM成像, 显示了界面处立方相和六方相的交错[59]
Figure 11 (a) Cross-sectional STEM image; Zoom and definition of (b) wurtzite zone and (c) cubic zone; FFT diffraction pattern of the area in the green box showing (b') wurtzite GaN and (c') c-GaN, where (110) faces the reader; local intensity maxima (111) and (111) make an angle of 70.5° relative to the origin, characteristic of the zinc-blende/cubic lattice. (d) STEM analysis and crystallographic directions. (e) Interface in the vicinity of the EG mask, showing both cubic and wurtzite phases on GaN, as well as the biphasic transition region. Reprinted from [Ref. 59], with the permission of AIP Publishing
图 12 MQW材料设计、转移流程图. (a) 在蓝宝石上生长单晶h-BN层后, 生长AlGaN缓冲层及MQW结构; (b) 将MQW结构倒置并与另一衬底通过In层叠在一起; (c) 热处理增强In层的结合性; (d) 通过机械方法剥离蓝宝石衬底, 完成MQW结构与外来衬底的结合[62]
Figure 12 (a) Single-crystal h-BN release layer growth is performed on a sapphire substrate, followed by growth of wurtzite AlGaN layer and the MQW structure. (b) The MQW structure is flipped upside down and placed on a foreign substrate via an adhesive indium sheet. (c) Heat-sealing of the indium, and then (d) the MQW structure is released from the host sapphire substrate by mechanical force and transferred to the foreign substrate. Reprinted by permission from Macmillan Publishers Ltd: [Nature] (Ref. 62), copyright 2012
图 13 MoS2对GaN生长的作用. SEM图像显示 (a) MoS2上生长的GaN; (b) Mo金属上外延生长的GaN[68]
Figure 13 Necessity of MoS2 for GaN growth. (a) Hexagonal crystals of GaN obtained on MoS2 flakes; (b) Faceted chunks of GaN on Mo substrates. Reprinted with permission from the author (Arnab Bhattacharya)
-

计量
- PDF下载量: 31
- 文章访问数: 1878
- HTML全文浏览量: 290